Share this Job
Process Operator job at Nile Breweries Limited | Apply Now
Are you looking for Engineering jobs in Uganda 2025 today? then you might be interested in Process Operator job at Nile Breweries Limited
Jinja, Uganda
Full Time
About the Organisation
Nile Breweries Limited (NBL), established in 1951 by businessmen associated with the construction of the Owen Falls Dam, has grown into Uganda's leading beer manufacturer, boasting a 59% market share and an annual production capacity of 2.45 million hectolitres from its breweries in Jinja and Mbarara. The company's purpose is to "Dream Big to create a future with more Cheers," aiming to serve up new ways to meet life's moments and make a meaningful impact in communities and the world.
NBL has earned recognition for its commitment to sustainability, notably winning the National Environmental Management Authority (NEMA) Award in 2012 for excellence in environmental protection. The company fosters a collaborative and inclusive work culture, offering employees opportunities for growth and development within the global AB InBev family. With a workforce of over 500 employees, NBL provides various job opportunities, which are regularly updated on their official website.
Innovation is central to NBL's business model, exemplified by the introduction of Eagle Lager in 2002, a sorghum-based beer crafted from local grains predominantly grown by smallholder Ugandan farmers. The company's core values emphasize quality, responsibility, and community engagement. NBL actively participates in corporate social responsibility initiatives, including supporting over 10,000 local farmers to grow and supply barley to its maltings plant and implementing sustainability goals aimed at holistic environmental and social impact. For more information, visit their official website at www.nilebreweries.com.
Job Title
Process Operator job at Nile Breweries Limited
Nile Breweries Limited
Job Description
Job Title: Process Operator (Fresher Jobs)
Organisation: Nile Breweries Limited
Duty Station: Jinja, Uganda
Duties, Roles and Responsibilities
Operating and Process Control
Operating sub processes of the Packaging plant according to the Standard Operating Procedures, supporting the plant control system and verifying that process control is being maintained
Assure quality of raw materials by monitoring conformance to Company and Regional Standards and any deviations corrected
Preparing plant for start-up by ensuring Brand and process changes correctly identified, al inputs are available including utilities, documentation and verified and calibrated equipment is available, and plant is visually inspected for availability to produce and set up in accordance with SOP’s
Starting and operating the Packaging process by complying with OH+S requirements whilst taking corrective action when deviations occur to prevent non-standard product. Ensuring that non-standard operations are documented and that the Concession/Permit procedures are fully adhered.
Shutting down the plant in accordance with WI and any deviations recorded.
Carrying out CIP cleaning, sampling and measuring CIP outputs, external cleaning of plant and work area, and visual cleanliness inspections.
Controlling inputs usage i.e. stock levels maintained as per region requirements, regular quality checks on stock, usage ratios checked, and all inputs stored in correct demarcated areas.
Ensuring plant availability via ensuring that scheduled maintenance plans happen, identifying ad hoc maintenance tasks and referring to others to correct, giving on-going assistance to Team members to identify root causes of breakdowns, observing required ‘lock-out’ procedures and other OH+S Act requirements.
Constantly reviewing process performance against target and recording short stops. Where process performance does not meet target, or trends indicate the existence of problems, corrective action must be initiated
Recording waste on the appropriate documentation or information systems and reviewing waste trends to identify problems or opportunities timeously.
Responding rapidly to upstream or downstream triggers that could result in out-of-control process situations.
Appropriate problem-solving approaches, as detailed in the problem-solving work practice must be followed.
Performing housekeeping tasks, applying 5s principles and following safe work practices. Unsafe work practices must be identified and corrected.
Assisting fellow team members in the execution of their tasks
Maintenance of Plant and Equipment
Carrying out in-depth cleaning, lubrication and inspection of plant equipment according to the Standard Operating Procedures and/or maintenance schedules.
Performing autonomous tasks, in accordance with the maintenance schedule, and where required requesting the assistance of an artisan.
Identify maintenance problems, and report these through to the team leader for resolution.
Assisting Packaging Artisans in executing running repairs on shift.
Completing all documentation including job cards, COSWIN notifications and other shift documentation.
Quality Control and Analysis
Carrying out the required quality checks/analyses as per Standard Operating Procedures and recording the results on the appropriate information system.
Constantly reviewing quality performance against targets and conducting trend analysis to identify problems timeously.
Coaching, mentoring, verifying and transferring knowledge whist providing assistance to fellow team members in the execution of quality checks.
Where quality problems have occurred, identifying and resolving them using the correct problem-solving approaches.
Communication
Actively participating in shift meetings, asking questions to test understanding and contributing suggestions.
Using gap lists to record issues, problems and improvement opportunities.
Understanding the team dashboards and participating in team target review sessions.
Making use of relevant communication media (e.g. shift logbook) to stay informed and inform others of issues.
Completing required hand over to incoming shift team members, ensuring the issues relating to plant performance, quality and maintenance are communicated
Problem Solving
When problems occur, applying the appropriate techniques (e.g Quick Fix Routines, 5 Why, etc.) to identify and correct the problem.
Where a problem cannot be resolved escalate to the team leader
Where problems have been resolved, verify that the problems have been eliminated.
Participate in, where required, team problem solving activities.
Continuous Improvement
Using Short Interval Control charts to review trends and to identify opportunities for the removal of waste and variation in the process.
Constantly seeking opportunities for continuous improvement and ensuring these are recorded on the gap list.
Participate in regional or divisional plant optimisation trials.
Voyager Plant Optimization Practices
Execute all shift routines in accordance with Voyager Plant Optimization principles.
Continuously improve own competence and support competence development of team members in accordance with the Global Competence Framework (commonly known as CAP).
Conduct self-management of own performance and participate in team and individual performance management practices in accordance with the company’s performance management system.

SERVICES
COMMERCIAL
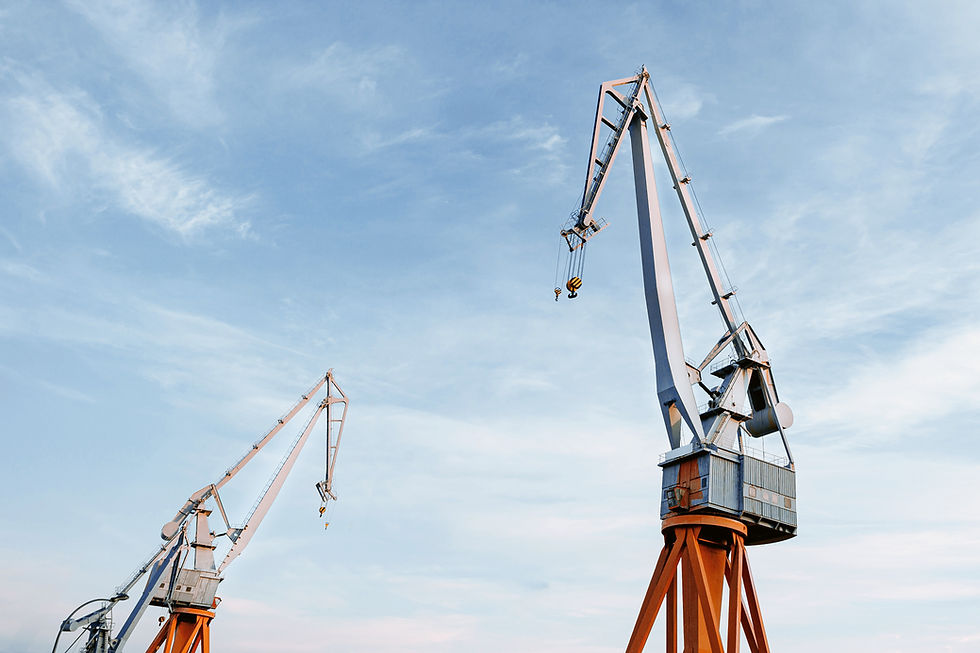
SERVICES
INDUSTRIAL

SERVICES
RESIDENTIAL

SERVICES
COMMERCIAL
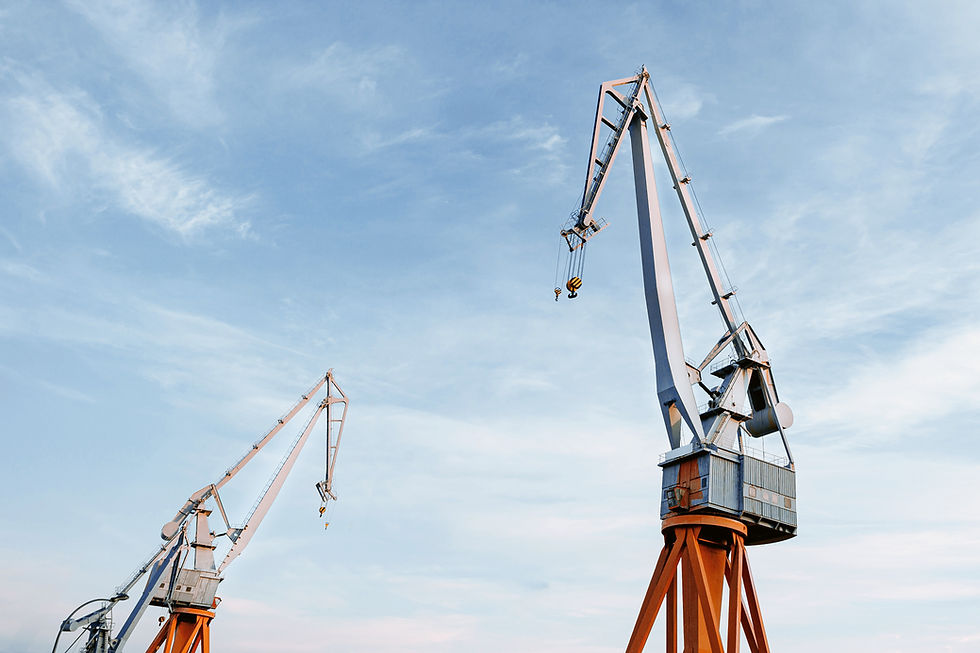
SERVICES
INDUSTRIAL

SERVICES
RESIDENTIAL

SERVICES
COMMERCIAL

SERVICES
COMMERCIAL

SERVICES
COMMERCIAL

SERVICES
COMMERCIAL
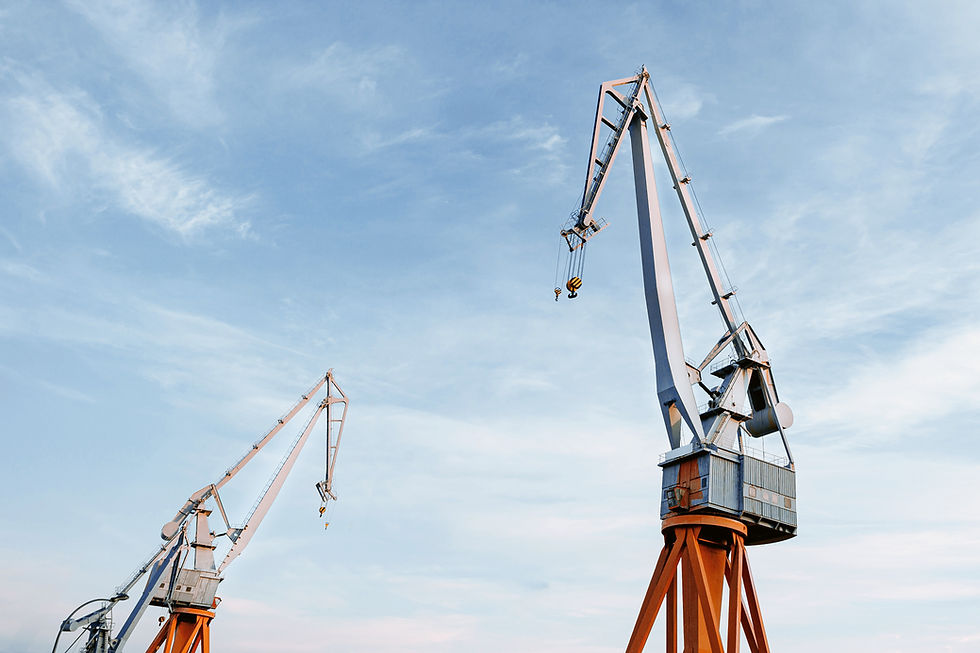
SERVICES
INDUSTRIAL

SERVICES
RESIDENTIAL
Qualifications, Education and Competencies
National Diploma in Electrical/Mechanical Engineering.
At least 2 years working experience in a FMCG industry.
Good knowledge of production processes and technologies
Familiarity with maintenance systems
Key Attributes and Competencies:
Team Player and a self-starter
Good communicator
Analytical, and is a Problem-solver who is willing to operate in an unstructured environment
Achievement-driven
Results-driven whilst taking accountability for his work area
How to Apply
All interested candidates who meet the above specifications should apply at the Apply Button below.
Deadline: 12th April 2025