Share this Job
3 QA Officer (Quality Assurance Officer) job at Microhaem Scientifics and Medical Supplies | Apply Now
Are you looking for administrative jobs in Uganda 2024 today? then you might be interested in QA Officer (Quality Assurance Officer) job at Microhaem Scientifics and Medical Supplies
Kampala, Uganda
Full Time
About the Organisation
Microhaem Scientifics and medical supplies Ltd, Trading as Microhaem Scientifics (MHS) was established in 2012 as a medical supplies company in Uganda.
We are one of the leading medical supplies company in East Africa now. We treasure quality, and we know that quality products save lives.Microhaem Scientifics (MHS) conducts medical supplies marketing, sales, installation, service, maintenance, repair and capacity building of medical personnel in the same fields as well research and consultancy.The company undertakes all maintenance duties for medical equipment instruments and all other repair services of the products it supplies and distributes.
Established in 2012, Microhaem Scientifics is the first indigenous IVD test Kits manufacturer in the Great Lakes Region of Africa and one of the leading medical supplies company strategically located in Kampala, Uganda. The company’s manufacturing portfolio includes Point of Care tests, Molecular Diagnostics tests and Research and development in the neglected tropical diseases.
Job Title
3 QA Officer (Quality Assurance Officer) job at Microhaem Scientifics and Medical Supplies
Microhaem Scientifics and Medical Supplies
Job Description
We are currently seeking a diligent and detail-oriented Quality Assurance Officer to join our client in the pharmaceutical industry. As a QA Officer, you will be responsible for ensuring that all products and processes adhere to quality standards and regulatory requirements. Your role will be vital in maintaining the integrity of our products and in upholding our commitment to producing safe and effective pharmaceuticals.
Duties, Roles and Responsibilities
Key Duties and Responsibilities:
Quality Compliance: Monitor and ensure compliance with all relevant regulations, guidelines, and industry standards for pharmaceutical manufacturing and quality control.
Documentation Management: Maintain accurate and organized documentation related to quality control processes, including batch records, standard operating procedures (SOPs), and quality testing data.
Batch Release: Review batch records and associated documentation to ensure that products meet quality specifications before release for distribution.
Quality Audits: Participate in internal and external quality audits to assess compliance with regulatory requirements and identify areas for improvement.
CAPA Management: Contribute to the identification and implementation of Corrective and Preventive Actions (CAPA) in response to quality issues, deviations, and non-conformances.
Root cause and investigation: Identify the gaps or deviations in the system and follow up to ensure that they are resolved.
Change Control: Review and assess proposed changes to processes, equipment, or procedures to determine their potential impact on product quality and compliance.
Supplier Quality: Collaborate with suppliers and vendors to evaluate their quality systems and ensure the quality of incoming raw materials and components.
Quality Training: Assist in the development and delivery of quality-related training programs for employees to enhance their understanding of quality principles and practices.
Product Complaints: Investigate and analyze customer complaints related to product quality and work with relevant departments to implement corrective actions.
Validation Activities: Support validation activities, including equipment qualification, process validation, and cleaning validation, to ensure that processes are capable of consistently producing quality products.
Risk Assessment: Participate in risk assessment activities to identify potential quality risks and develop strategies to mitigate them.
Continuous Improvement: Contribute to the continuous improvement of quality systems by identifying opportunities for streamlining processes and enhancing efficiency.
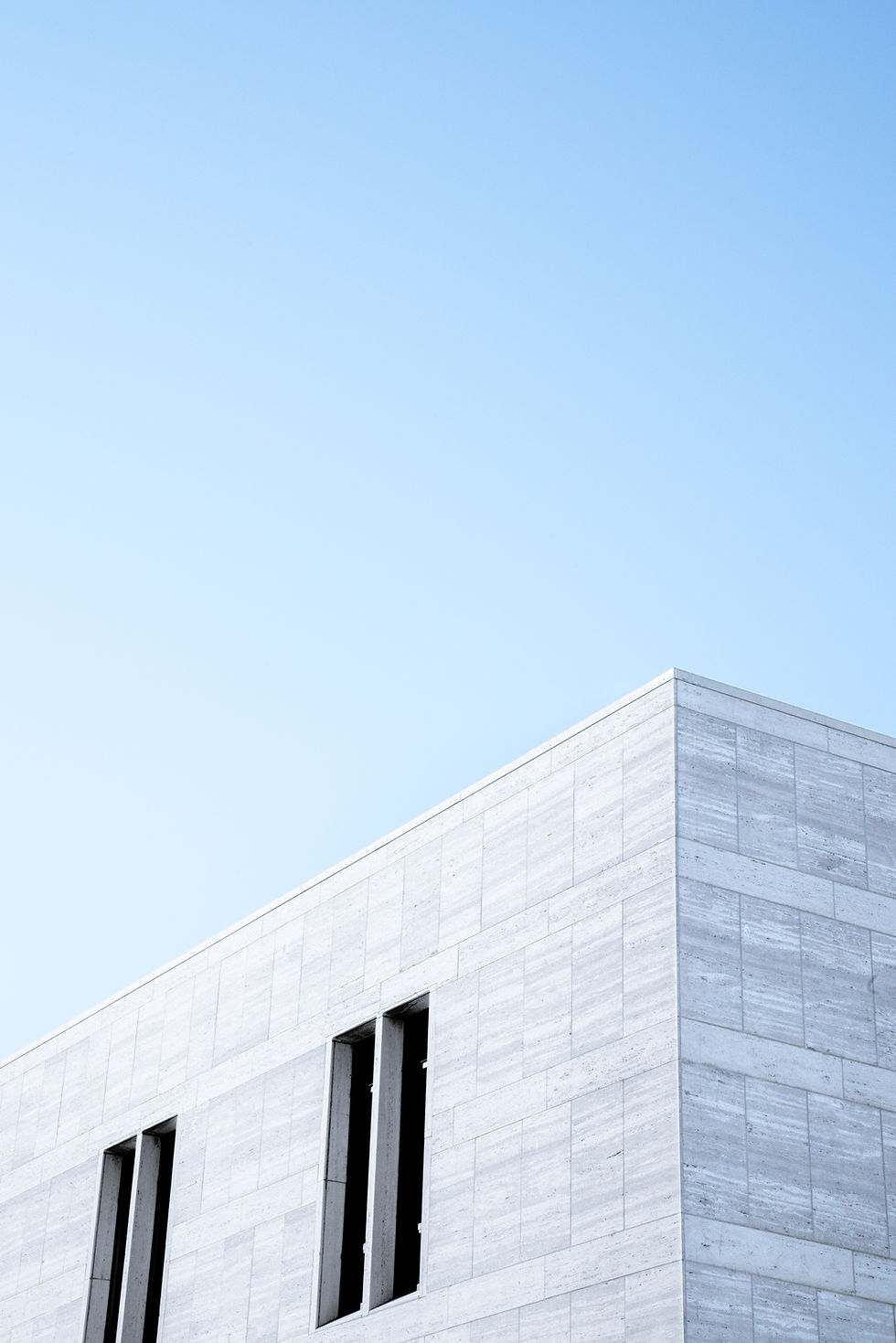
SERVICES
COMMERCIAL

SERVICES
INDUSTRIAL

SERVICES
RESIDENTIAL
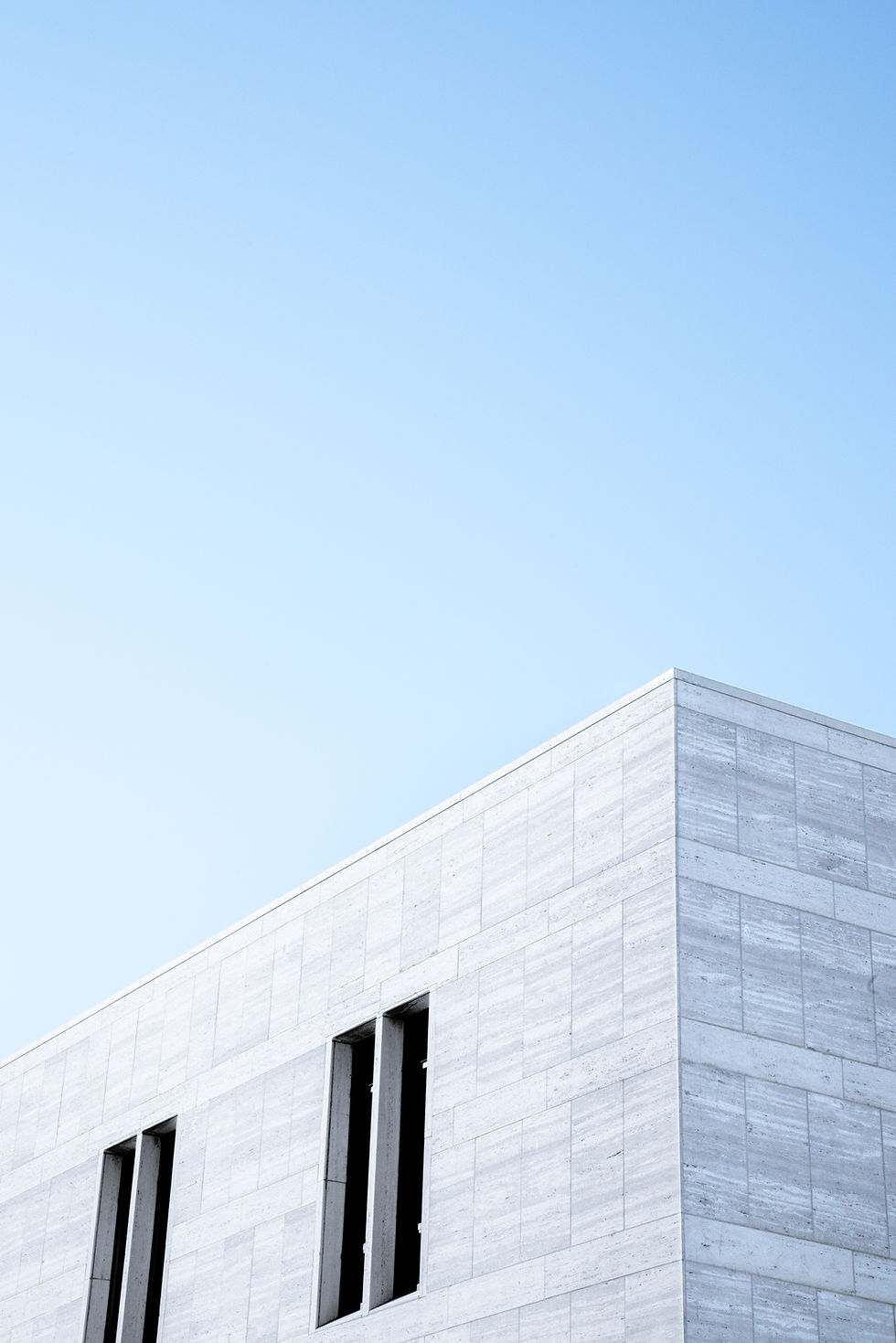
SERVICES
COMMERCIAL

SERVICES
INDUSTRIAL

SERVICES
RESIDENTIAL
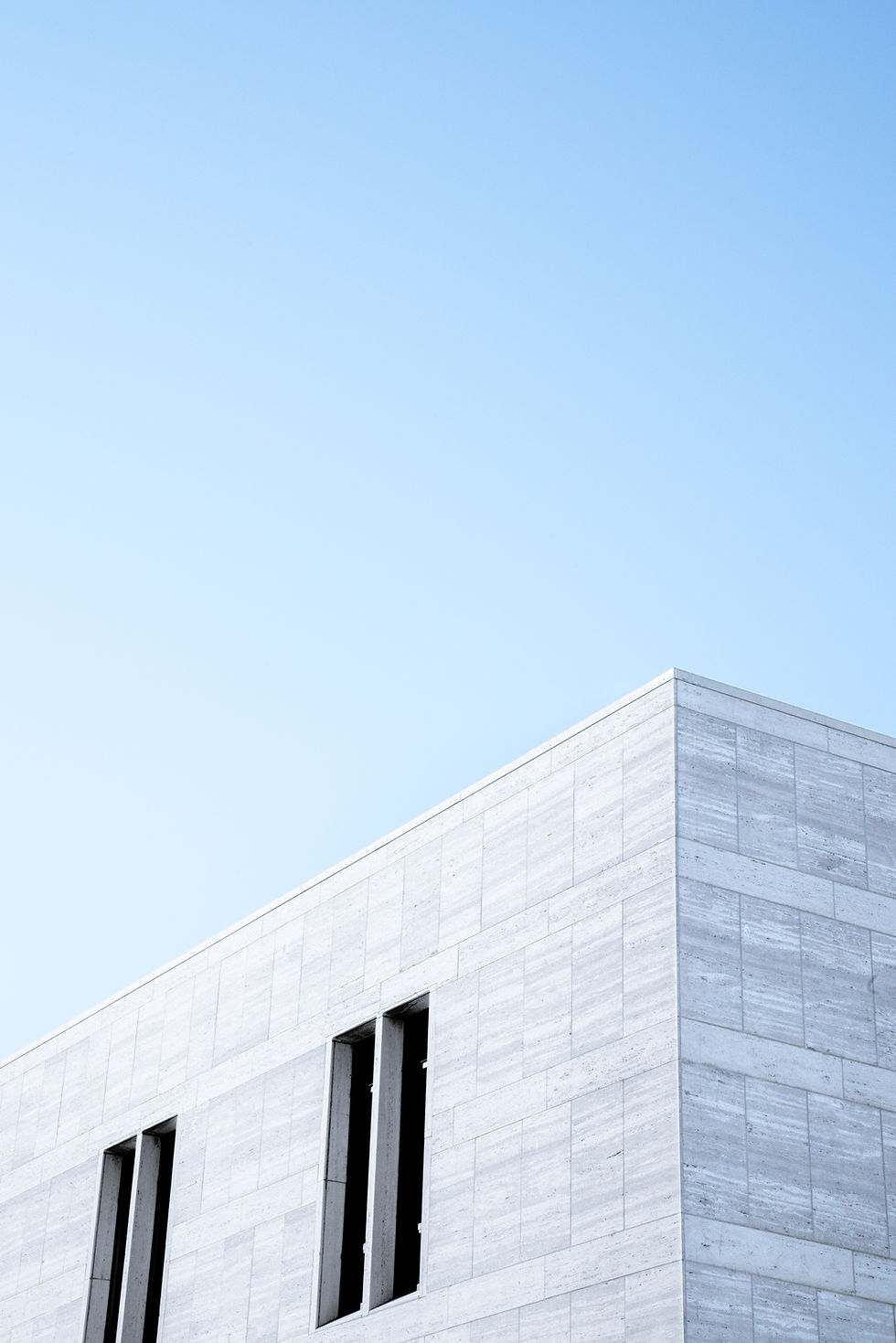
SERVICES
COMMERCIAL
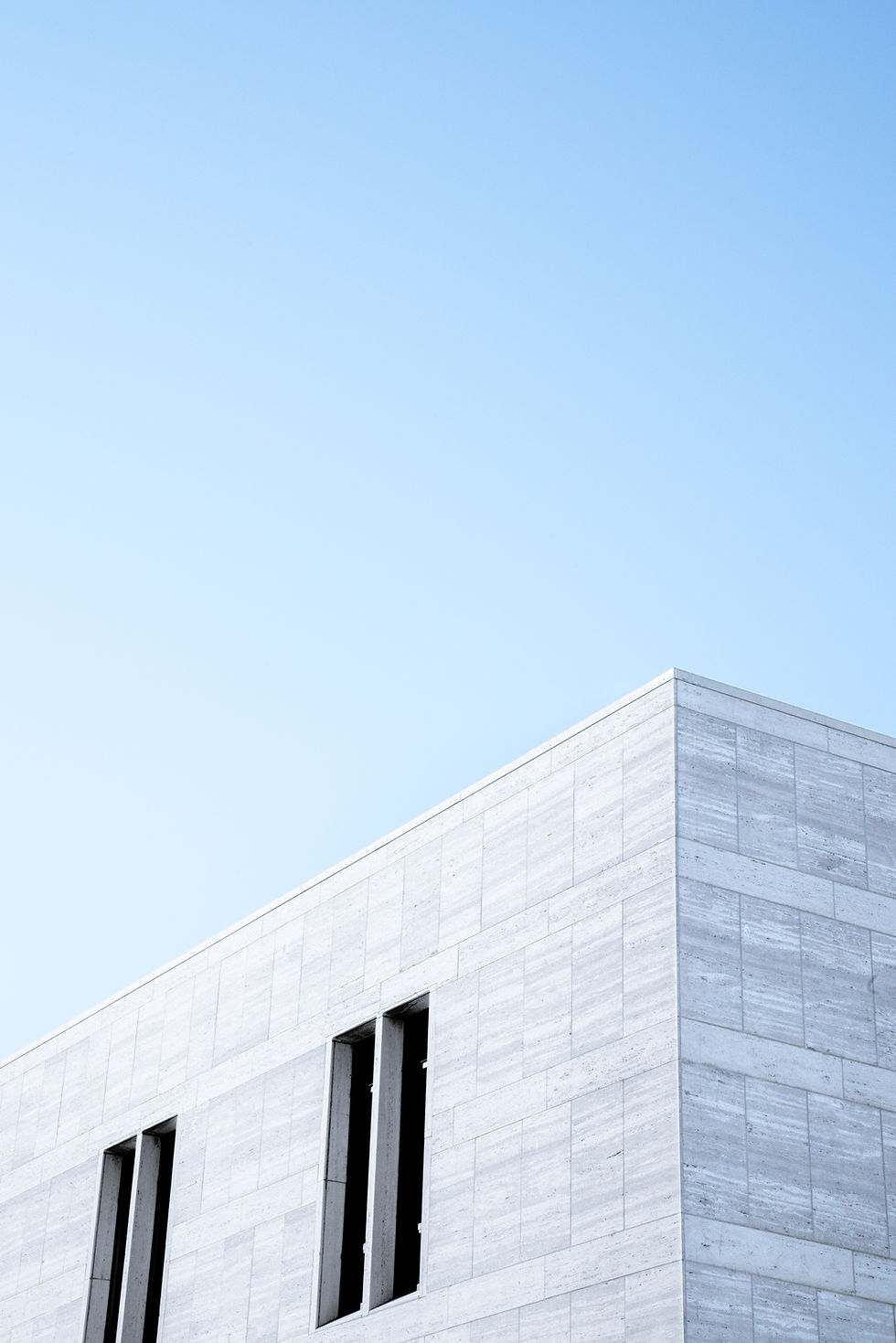
SERVICES
COMMERCIAL
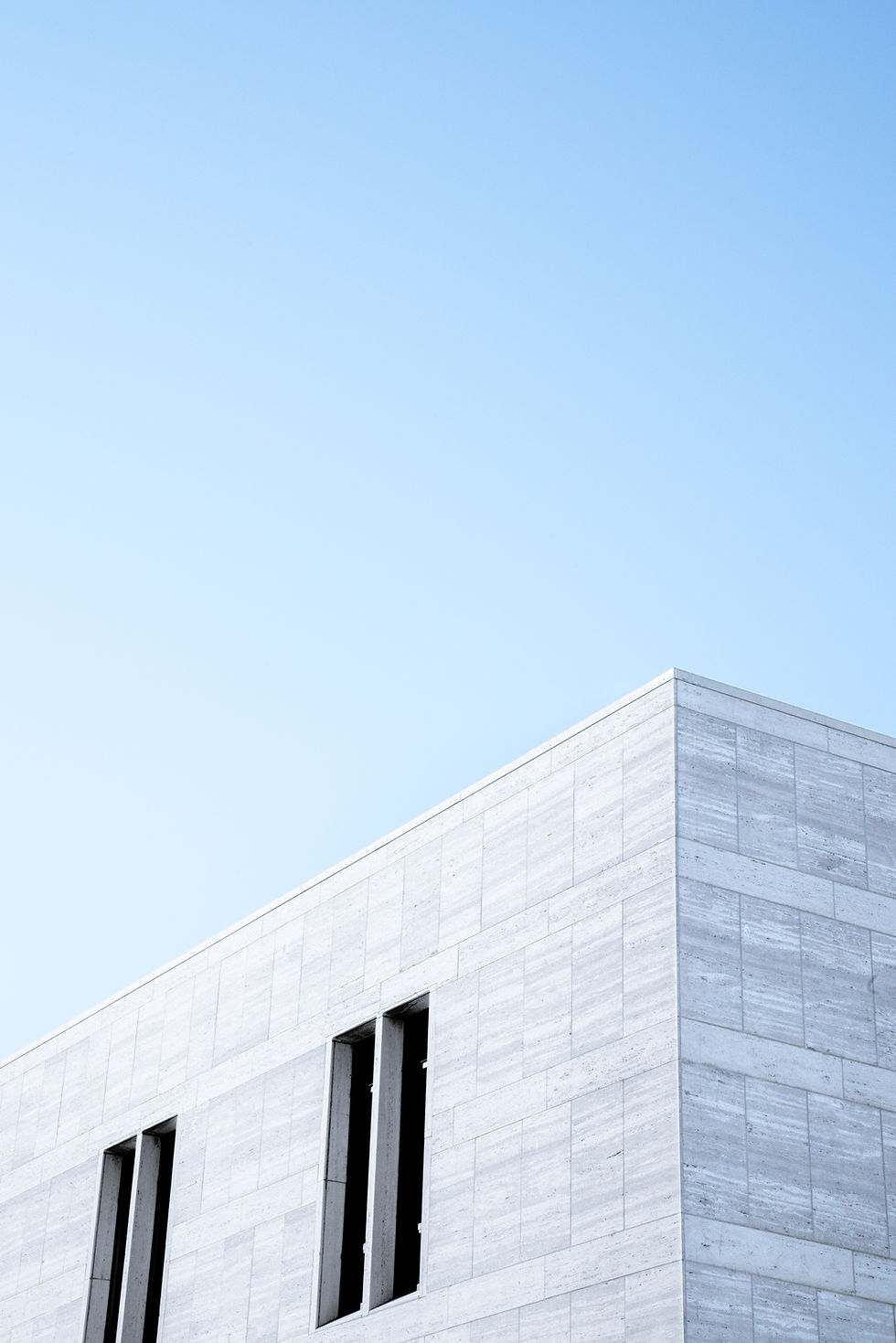
SERVICES
COMMERCIAL
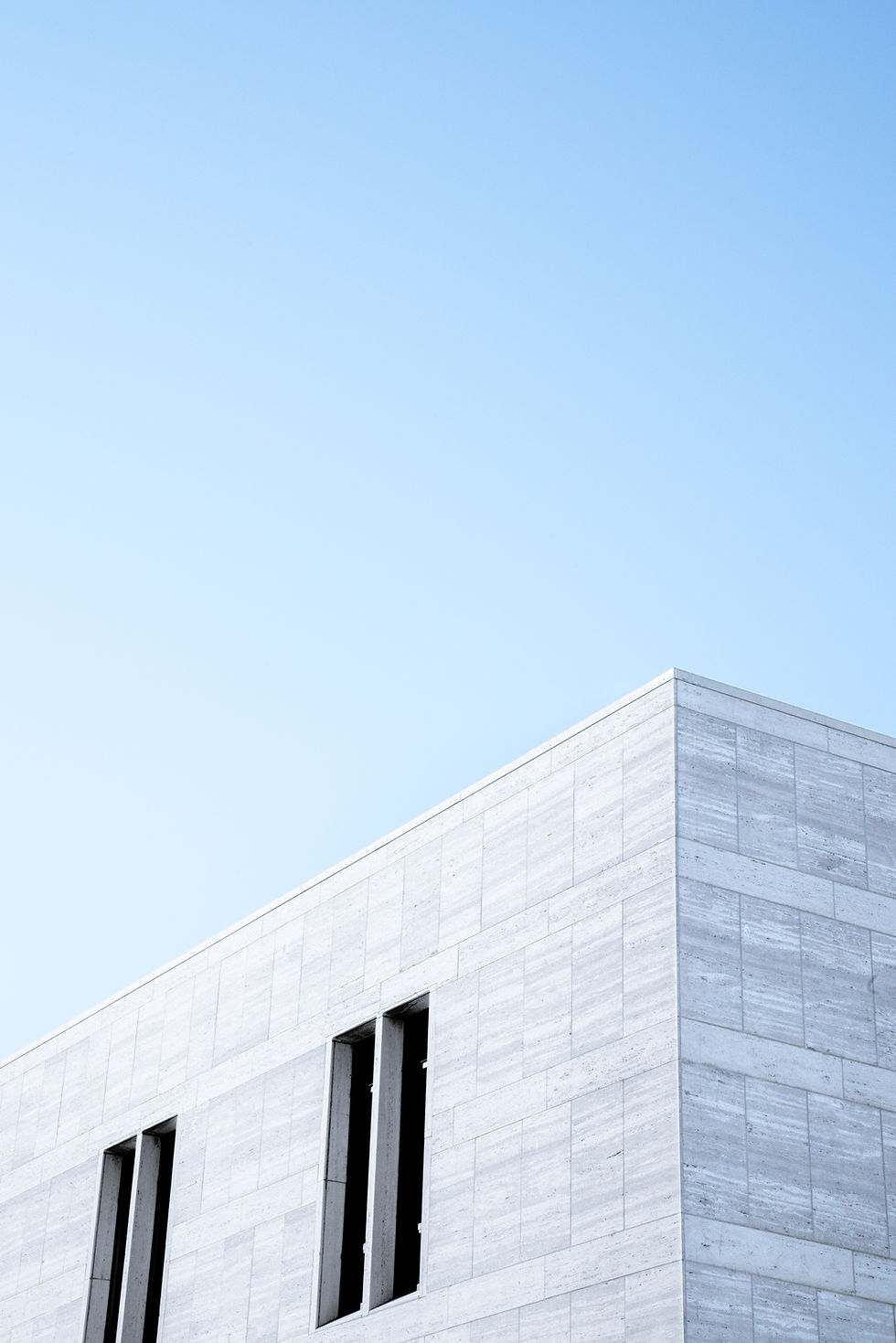
SERVICES
COMMERCIAL

SERVICES
INDUSTRIAL

SERVICES
RESIDENTIAL
Qualifications, Education and Competencies
Qualifications, Skills and Experience:
Bachelor’s degree in Medical/Pharmacy/Biomedical Engineering or related fields.
Strong information retrieval and data analysis skills, as well as excellent official document writing abilities;
Strong resilience, ability to face challenges and adapt to new things.
Previous experience (3+ years) in quality assurance within the pharmaceutical or related industry.
Familiarity with pharmaceutical regulations and guidelines, such as Good Manufacturing Practices (GMP) and International Council for Harmonisation (ICH) guidelines.
Strong attention to detail and analytical skills to assess quality data and trends.
Experience with quality management systems and documentation practices.
Problem-solving abilities to address quality issues and implement appropriate solutions.
Knowledge of risk assessment and root cause analysis methodologies.
Certification in Quality Management or Quality Assurance is desirable.
How to Apply
Send the following requirements to recruitment@microhaem.co.ug
Application letter
CV/Resume with at least 3 referees
Academic documents
Deadline: 11th November 2024